袋装食品快速自动分拣系统设计
南京工业职业技术学院 陈亚琳,宋增禄
摘要:食品加工企业加工的食品种类众多、差异较大,从而导致食品分拣较为困难。为提高食品分拣效率、提升食品加工设备的自动化程度,以并联机器人和机器视觉为基础,设计一种机器视觉的食品快速自动分拣系统。通过CCD工业相机和图像采集卡对食品图像进行采集处理,处理后的图像将信息输出并控制并联机器人进行动作,在硬件结构基础上对分拣系统软件进行设计。结果表明,该分拣系统能够实现不同食品的快速分拣,大幅提升食品分拣效率,降低工人劳动强度。
关键词:食品加工;分拣;并联机器人;机器视觉
食品加工企业通常同时生产多种食品,如饼干、糖果等,在初期的食品生产中机械设备生产效率较高,而后续包装机械往往生产力较弱,因此需要通过分流装置对食品进行分流,同时对不同食品及外观质量进行分拣。
传统的食品分拣通常通过人工进行分拣,但人工分拣通常效率低、劳动强度大,卫生不能有效保证,直接影响食品加工企业的经济效益和产品质量。因此有必要开发一套自动、智能检测系统,该系统对于提高企业自动化程度、提升企业生产效率、提高产品质量具有现实意义。
机器视觉分拣技术是利用计算机摄像技术模拟人眼的视觉,将图像采集到图像处理系统中,图像处理系统将分析图像中的关键信息,并通过获取的信息做出判断,进而再控制机械结构将产品挑出。基于机器视觉的食品分拣系统主要由图像采集设备、光学系统、图像处理系统、机器人及人机界面等众多系统共同组成。将机器人、机器视觉等智能控制技术引入到现代食品加工生产中,利用机器视觉对食品进行实时检测和分拣,利用机器人的高速性可以显著提高食品分拣效率,降低工人劳动强度,提高产品质量。
在并联机器人中引入机器视觉检测技术,通过机器视觉图像处理技术实现并联机器人的智能自动控制,通过并联机器人将不同食品进行分拣。试验数据表明,机器视觉的袋装食品分拣系统能够快速地将食品进行分拣,大幅提升食品加工企业生产效率。
1 自动分拣系统
机器人分拣系统组成原理如图1所示。机器视觉并联机器人分拣系统主要包括并联机器人、工业计算机、CCD工业相机、图像采集卡、运动控制卡、抓手等。以工控机作为系统的上位机,利用CCD工业相机采集传送带上方的食品图像;通过图像处理,对食品进行定位、跟踪、抓取。运动控制器作为下位机,利用运动控制卡实现并联机器人的多轴控制,通过并联机器人实现食品的抓取、分装。
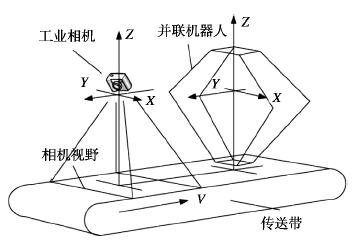
图1 机器人分拣系统组成原理
1.1 并联机器人系统
并联机器人系统主要由机器人本体结构、机器人抓手、示教手操器及各伺服驱动电机等构成。机器人末端抓手主要通过启动吸盘吸取或气动抓手,通过抓手完成食品的抓取。
1.2 机器视觉系统
通过工业CCD相机完成传送带上方食品图像的采集,并将采集到的图像传送到计算机系统中,计算机系统利用图像处理算法,对获取的图像进行处理,根据处理的结果对机器人发送相应的动作指令。
2 分拣系统硬件设计
机器视觉的食品快速自动分拣系统是一种多技术相结合的智能分拣方式,涉及光源照明技术、图像采集技术、多轴同步控制技术等。光源照明技术作为图像采集系统中非常重要的一部分,光线的强弱直接影响采集图像的质量,而光电技术主要是CCD相机镜头的选用,在CCD相机镜头选择上尽量保证镜头最高分辨率的光线与照明波长CCD接收的波长相匹配。图像采集卡是高速图像处理中必不可少的元件,采集卡将相机获取的图像传送到处理器中,处理进一步对图像进行一系列处理。并联机器人驱动系统主要是针对伺服电机,伺服电机对位置和速度的控制较准确,通过伺服驱动技术可以实现机器人的快速运动和快速定位。机器视觉分拣系统硬件主要包括光源、CCD相机、图像采集卡、伺服电机等,硬件结构如图2所示。
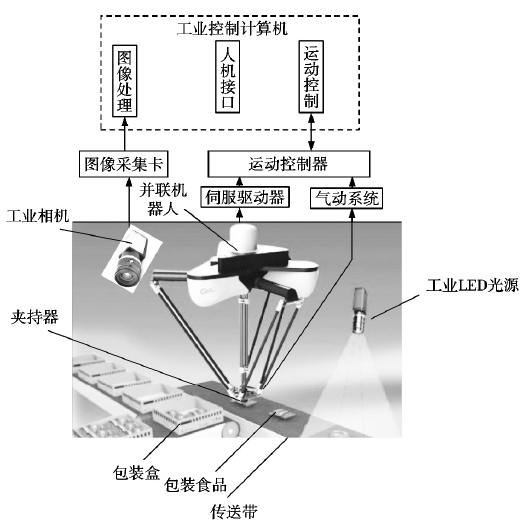
图2 分拣系统硬件结构
2.1 光源
对于光源的选择需要综合考虑,如光照强度、均匀度、光源寿命等,通过光源使得食品外部特征尽可能图像出来,便于区分待测物品和背景。综合比较多种光源,选择LED灯作为采集系统照射光源,该光源亮度较大,使用寿命较长且耗电量较低,发热较小、照明均匀。
2.2 CCD相机
2.2 CCD相机
相机选择时不仅需要考虑其工作性能是否能够满足检测系统的设计要求,还要兼顾其数据传输过程中是否对系统产生影响。相机选型过程中综合考虑分辨率、图像传输速度、曝光时间及接口形式等。试验选择方诚公司型号IK145M-15CCD机,相机具体参数如表1所示。
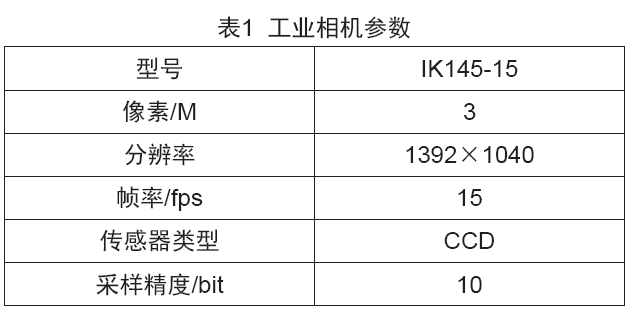
2.3 图像采集卡
图像采集卡作为图像采集和图像处理的桥梁,CCD相机将获得的食品图像传送到图像采集卡中,图像采集卡再将图像传送到计算机处理器中,系统中采用NI公司生产的PCI-1426图像采集卡,该采集卡通过PCI接口与计算机进行数据交互,相机接口采用Camera Link标准,该接口传输速度快,可以进行高速图像采集,采集卡如图3所示。
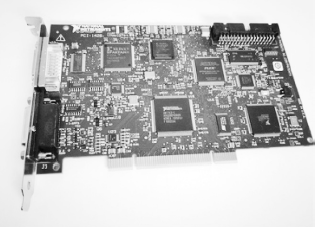
图3 图像采集卡
3 分拣系统软件
合理的软件架构设计是整个系统软件程序编写的必要准备,为使程序具有可读性及可修改性,控制系统软件采用模块设计方法,分拣系统软件主要分为主模块、机器视觉模块、图像处理模块及并联机器人运动控制模块,软件系统结构如图4所示。
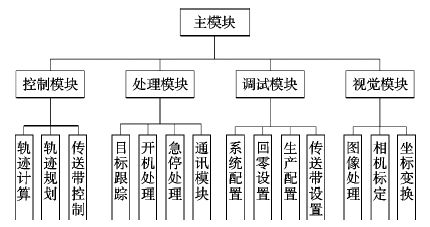
图4 软件系统结构
程序的主模块主要负责各子程序的调用及与上位机的通信,调试模块主要完成系统参数配置、机器人原点搜索、传送带速度设定;视觉模块主要是完成食品图像采集,经过图像处理后得到袋装食品坐标位置信息,通过坐标转换得到机械手需要运动到目标位置;处理模块主要完成食品目标跟踪、通讯处理、紧急停机处理等;控制模块主要完成机器人轨迹规划、速度规划及机器人示教等。
根据袋装食品生产流程以及控制系统要求,搭建控制系统软件,控制系统软件框架如图5所示,机器上视觉袋装食品分拣软件具体流程为:
1)控制系统上电后,程序进行初始化处理,将数据进行初始化,如计时器及各种数据寄存器,调用部分参数设置模块,将初始化参数写入已经清零的数据寄存器中,完成开机准备工作并调用开机模块程序。
2)视觉模块程序采用不断循环的方式,当袋装食品进入到相机视线相机对食品进行拍照,拍照后图像经过图像采集卡传送到计算机中并由坐标转换程序将其转换为机械手末端坐标系下的数据。
3)经过视觉图像处理后对并联机器人发出动作指令,机器人开始规划最佳运动路径,控制器开始调用运动控制程序,通过运动控制模块驱动机器人各手臂运动完成袋装食品的分拣任务。
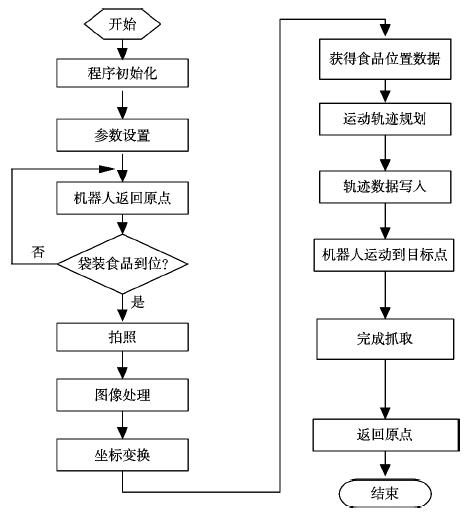
图5 机器视觉分拣系统软件架构
4 试验分析
为验证机器视觉袋装食品快速自动分拣系统的有效性,搭建分拣系统进行实验验证。将袋装食品按照一定顺序存放在传送带上,并由传送带一次将食品传送至视觉系统中,机器人通过视觉系统控制方案对袋装食品进行分拣,机器人分拣过程如图6所示。传送带每分钟可以传送110包食品,袋装食品之间间隔根据传送带传送速度进行设定。分拣系统指标要求如表2所示。
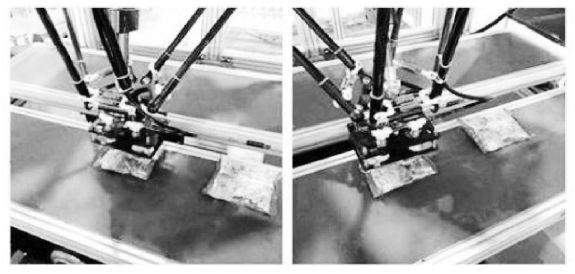
图6 机器人分拣过程
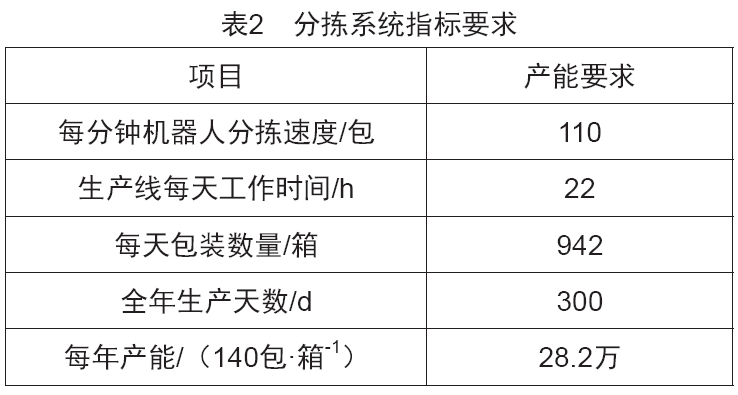
通过统计,单台机器视觉机器人分拣系统平均每分钟可实现120包的抓取速度,能够达到每台单独抓取110包的产能指标要求。
5 结语
为提高袋装食品分拣分装速度、提高生产企业生产效率、提升企业经济效益,将并联机器人与机器视觉系统相结合,设计一种基于机器视觉的分拣系统。分拣系统的总体设计主要包括分拣系统的工艺流程分析、控制系统硬件平台的搭建,并在硬件结构基础上详细对分拣系统软件进行设计,通过模块设计方法,大幅提高分拣系统软件可读性及可编程性。结果表明,该袋装智能分拣系统能完成既定设计目标,提高食品生产效率,降低工人劳动强度。
免责与声明
1.凡注明有“【独家】”的内容,其所有权均属“中国肉类机械网”所有。
2.凡转载本网“【独家】”内容,需与本网联系,并注明信息来源“中国肉类机械网”,违者将追究法律责任。
3.凡本网编辑转载的信息内容,旨在传递更多信息,并不代表本网赞同其观点和对其真实性负责。
4.如涉及作品内容、版权和其它问题,请在15日内与本网联系,我们将在第一时间删除内容并表示歉意!
5.版权&投稿热线:电话:010-88131969,传真:010-88131969,邮箱:mpmpcweb#126.com(注#换成@)
2.凡转载本网“【独家】”内容,需与本网联系,并注明信息来源“中国肉类机械网”,违者将追究法律责任。
3.凡本网编辑转载的信息内容,旨在传递更多信息,并不代表本网赞同其观点和对其真实性负责。
4.如涉及作品内容、版权和其它问题,请在15日内与本网联系,我们将在第一时间删除内容并表示歉意!
5.版权&投稿热线:电话:010-88131969,传真:010-88131969,邮箱:mpmpcweb#126.com(注#换成@)