刀具系统部分
在猪屠宰过程中,对猪胴体进行劈半一直是人工操作,靠专用弓形带锯将猪胴体锯切为二分体。其优点是费用成本低,缺点是工人劳动强度大,操作技术要求高,效率较低。尤其是锯切会产生骨肉消耗形成碎屑,一旦冷却不充分还会出现骨肉切面发热变质现象。
国产自动劈半机是近几年吸收国外先进技术进行转化设计的新型屠宰设备,因为它具有效率高、自动化程度高,博得猪屠宰企业的青睐。但是,由于种种因素制约,百分之百造仿是不可能的。在设计、制造方面还存在某些误区,导致在劈半质量、效率、可靠性、维修性、故障率等方面存在缺陷或不易发现的隐患。给制造者和使用者都带来负面影响。在此笔者将先行论证劈切式自动劈半机的刀具系统,或许能够起到抛砖引玉的效果。以后再对其它功能部位进行剖析。
刀具系统是自动劈半机的核心,自动劈半型式目前有圆锯劈半和双刀劈半两种。如引深分析,还可能会衍生出带锯自动劈半和单刀自动劈半型式。本文先就双刀劈半的刀具系统的设计作一阐述,希望与同仁共享。
刀具系统的设计应侧重:刀具结构与制造、刀臂设计与效率、尾部铰链、刀具尺寸与角度、安装关系与精度、劈切效率等几个方面。
一、刀具结构与制造
1、双刀劈半的刀具由两个互为180度的对称偏心动力轴驱动,高速交替沿倾斜的立椭圆轨迹进行劈切。特点是沿椭圆长轴方向运动时线速度较高,而且到达止点立即向反方向运动,转动惯量大即成为有破坏性的焦点问题。所以,应该首先考虑优化、降低刀具重量。
2、因为刀刃长度、刀具长度都与其它部件相关,所以变化余地不大。能够减量的部位将是刀背轮廓和刀具厚度。
3、因为刀柄尺寸已定,在满足两刀相互依靠、定位的条件下,刀背可以适当降低,除紧刀孔、退刀孔、提刀孔外,刀体上半部可以加工几个较大的弧形凹陷区,既明显减轻刀的重量,又不会妨碍劈切,不会藏污纳垢,不会降低刀体强度。
4、快速换刀以杜兰德结构方案为最佳,采用楔形燕尾型式,换刀时只需抬起外定位臂、放松紧定螺钉、拉出定位手柄,即可用退刀孔退下刀具。装入新刀后推入手柄、旋紧紧定螺钉即可,整个过程约两分钟,其它方案都会为之逊色。紧刀结构可分弹入型和弹出型。快速装卸又紧固可靠,这是衡量机型优劣的关键项目之一(右图)。
5、刀柄双燕尾交角约22度。燕尾截面角度为55度,如有成型刀具,也可为60度。必须有工艺、工装保证,加工才会由难变易。
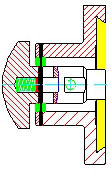
弹出型紧刀机构
首先要制作标准的配偶样板,刀臂与刀柄燕尾加工时分别
用样板检验和配研。进行配合涂色检验,接触面不低于70%,如工艺手段到位,紧刀孔和退刀孔可以与燕尾一次加工完成。
二、刀臂设计与效率
1、动力轴中心位置关系到刀具劈切行程和动力消耗。劈切行程、偏心量、劈切频率组成劈切效率的三要素。设刀臂杠杆总长为L,动力轴中心至铰链距离为L1,则L1与 L的关系按黄金分割比例分配,最大不应超过2:3(下图)。
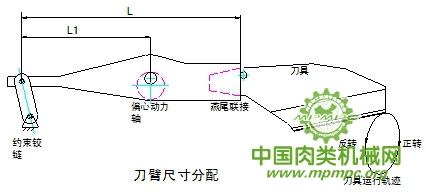
2、单刀劈切深设为t(mm),即椭圆纵长的二分之一。设频率为360,则单位时间内的劈切长度T=S×360(mm/s),T值必须大于刀箱垂直下降速度L(mm/s)。
如果T值偏小,而下降速度L增大时劈砍效果会大大降低。当T<L时撕割现象增大,与单面刃劈切分力合成,造成切口不直而呈瓦楞弧状(右图),与锯切劈半的效果形成了巨大差异。同时,撕割现象还会增大刀具刀臂系统的负荷。
3、令T值增大的途径是:加大偏心量和提高劈切频率。
三、尾部铰链
1、尾部铰链是配合偏心轴运动而摆动的杠杆约束支点,由于摆动频率较高,所以内部设有轴承,同样要求应降低运动惯量,使其重量力求达到最轻。
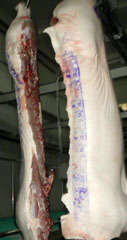
瓦楞弧状切口
2、众所周知,运动惯量大有利于转动的场合,使之匀速还可以储存并节省动力。而摆动则完全与之相反,运动惯量大会在高速返回时储存的巨大正能量变为负能量,会使系统超载,以致损坏刀臂、刀具、轴承系统。
3、事实证明,有的机型将后铰链尾部延长并增设重锤,其方案实为南辕北辙、事与愿违,既浪费了材料又置入了隐患。
四、刀具尺寸与角度
1、在材质、硬度等同的情况下,刀具角度设计合理与否关系到刀具锋利程度和耐用度。采用刀具用合金钢,刃部硬度满足HRC56~60并严格进行消除应力处理。刃部角度借鉴砍骨刀的特点,具有锋利的锋刃又保证足够的楔角,锋刃做成最大楔角形成刃带,推荐刃带宽为1~2毫米,楔角25~30度。其余部分刀体楔角5度,过渡楔角9度,
刀具厚度推荐尺寸为10mm(右图)。
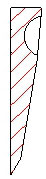
刀具角度
2、楔角也是关系到刀具强度的重要指标。楔角过大可以使耐用度提高,但带来的弊病是刀具锋利度降低,单面横向分力增大,易造成劈切不直或胴体的瓦楞弧状切口,劈切阻力、动力消耗增大,刀臂容易受损。
3、楔角过小可以使刀具锋利度提高,劈切阻力减小,但带来的弊病是刃部容易崩刃,使耐用度降低。
4、刀具大平面的平面度误差应不大于0.05mm,刃部经过研磨,其粗糙度误差不大于0.8μm。
五、安装关系与精度
1、劈切系统沿垂直导轨运行,同时又沿水平导轨纵向运行。水平导轨为一次基准,所以选择垂直导轨为二次基准。首先要求驱动轴中心与二次基准垂直。
2、刀具劈切方向应与刀具大平面一致,都与驱动轴中心线保持垂直,这一点至关重要,
3、两刀对称相依,静止时两平面可以有微量间隙,劈切时产生单侧分力。
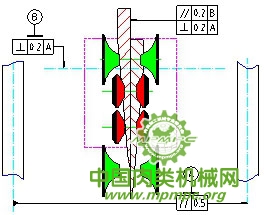
安装关系与精度
会使其自动靠紧、相互摩擦。两平面平行度误差应≤0.05mm。
4、检测量具可选用水平仪、百分表(配磁力座)、精密直角尺、塞尺等量具,通过手动,检验静态精度和动态精度。
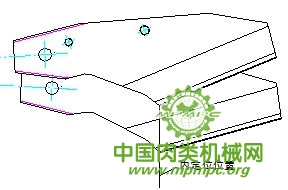
刀刃内端与内定位关系
5、动力正反转都可以工作,立椭圆轨迹的下一半即为劈切范围,可以正转或反转劈切, 只是在椭圆哪一侧劈切的问题。确定旋转方向之后,劈切时刀刃内端应与内定位垂直位置一致,只有这样才能发挥全部刃长的劈切功能,使劈切厚度实现最大化。
六、劈切效率
劈切效率除既定参数和以上几个因素外,还有速度的设定。除与输送机同步跟踪速度外,其它均设定为最高速,以实现最高劈切效率。因双刀劈切受机型、结构原理所限,能够接近400头/分即为比较理想的能力状态。