摘要:为了提高畜禽骨的粉碎率,以促进畜禽骨的回收利用效率,本文以猪骨为原料,比较了高压处理和酶解次序对猪骨粉碎率的影响,并对猪骨高压处理后的酶解工艺采用响应面法优化和对所得骨粉的钙、磷营养物质含量进行了测定。结果发现,猪骨经高压处理后再酶解所得粉碎率较高压处理前酶解所得粉碎率高;响应面法优化猪骨高压处理后的酶解工艺,得出酶解温度为55℃、酶解时间为2.01 h、pH 为7.00、加酶量为10363 U/g 时所得猪骨的粉碎率最高(82.0%),比未优化前提高了9.45%;对粉碎前后猪骨中钙磷营养物质含量分析,得出高压和酶解辅助机械粉碎对猪骨中钙磷损失小。总之,高压处理后酶解辅助机械破碎法有效提高了猪骨的粉碎率,所得骨粉的钙磷营养物质与原始猪骨中的钙磷含量相似。
关键词:骨素;酶解;木瓜蛋白酶;畜禽骨
畜禽骨是畜禽加工最主要的副产物。2013年我国的肉类总产量8373万t,位居世界第一。以畜禽骨约占胴体重10%~30%计算,2013年产生的鲜骨约837~2512万t 左右。畜禽骨的营养丰富,如果不对这些骨副产物有效利用,不仅造成资源的极大浪费,而且还会因为骨头富含营养物质易腐败变质而污染环境。因此,回收利用畜禽骨对畜禽加工业高效、可持续发展非常重要。目前,国内外研究人员开展了很多利用畜禽骨的途径,如将畜禽骨磨粉制作饲料,提取骨胶原蛋白等,但是均因为畜禽骨硬度较高、难粉碎而导致利用率低。
畜禽骨中含有大量的骨胶原蛋白是导致其难粉碎的主要原因。如果利用化学水解法使骨头软化,不仅会降低骨头的营养价值,而且还会造成钙的严重流失。若直接食用,比如熬骨头汤等,钙溶出率太低。因此,在最大程度保留畜禽骨中营养物质的同时将畜禽骨粉碎,对畜禽骨的回收利用非常急需。研究发现,酶解法可以使骨中的蛋白质分解,如Michel Linder 等人酶
解小牛骨回收骨蛋白,Benjakul 利用中性和碱性蛋白酶水解牙鳕的废弃物回收蛋白质,赵妍嫣等人用胰酶和木瓜蛋白酶混合酶解猪板骨提高骨的钙溶出率等。此外,研究发现高压和热处理可以使蛋白变性和分解,但将酶解和高压处理结合以提高畜禽骨粉碎率的研究较少。牡蛎壳等贝类经粉碎后过400目筛可获得超微骨粉颗粒,此时超微骨粉的消化吸收率得到了很好改善。因此,本研究以猪骨为原料,利用酶解和高压辅助机械破碎制备超微骨粉,以制备超微畜禽骨骨粉。
1 材料与方法
1.1 材料
新鲜猪脊骨和臀骨购于明蜀新村十陵菜市场。木瓜蛋白酶购于郑州龙生化工产品有限公司,酶活50万U/g。
1.2 实验方法
1.2.1 超微骨粉制作流程
猪骨→去肉、破碎→高压处理→酶解→胶体磨粉碎处理→分离→干燥→骨粉
1.2.2 猪骨的预处理
将新鲜的猪脊骨和臀骨去肉,手动剁成约1cm×1cm 的小方块。
1.2.3 高压处理
称取100g 骨块加入高压锅,以骨水比1:30 (m/m)混合,高压处理90 min。高压处理时间以高压锅开始沸腾时计算。
1.2.4 酶解处理
用木瓜蛋白酶对高压处理后的骨水混合液进行酶解,加酶量、酶解温度、酶解时间及酶解pH 值见表1。
1.2.5 胶体磨处理
用X-250两级胶体磨对酶解猪骨进行超微粉碎。粉碎时将胶体磨上刻度调至6,下刻度调至5,循环磨碎3次。
1.2.6 分离及干燥
将经过胶体磨处理的骨浆直接过分样筛,分样筛的目数依次为40目、60目、100目、120目、140目、160目、180目、200目、250目、300目、350目、400目,收集过400目筛的样品,将收集物置于ZFA-D5140鼓风干燥箱于80℃干燥至衡重。
1.2.7 粉碎率计算
以通过400目筛的骨粉重量占整个骨头重量的百分率评价粉碎程度。粉碎率η的计算式如下:
Η= m400 /mtotal×100%
注:m400 指过400目筛的骨粉的质量,单位为克(g);mtotal骨头总重,单位为克(g)。
1.2.8 猪骨中钙、磷含量测定
猪骨中钙含量测定按照GB/T 9695.13-2009 中滴定法测定,磷含量根据GB/T 9695.4-2009 中分光光度法测定。
1.2.9 响应面设计
采用5中心、4因素、1相应、21次试验、Hartley法设计试验方案,各因素编码及水平见表1。
表1 响应面因素编码及水平
温度 (TEM)/℃ | 时间 (TIM)/h | pH | 加酶量 (EN)/(U/g) | |
-1.68179 | 40.00 | 2.00 | 4.00 | 5000.00 |
-1 | 46.08 | 2.61 | 4.61 | 6418.89 |
0 | 55.00 | 3.5 | 5.50 | 8500.00 |
1 | 63.92 | 4.39 | 6.39 | 10581.11 |
1.68179 | 70.00 | 5.00 | 7.00 | 12000.00 |
1.3 数据处理与分析
用EXCEL2010和SAS9.0对数据进行统计分析和响应面实验方案设计。
2 结果与讨论
2.1 酶解和高压处理次序对粉碎率的影响
为了分析酶解和高压处理次序对粉碎率的影响,对猪骨进行高压处理前和高压处理后,在固定料液比为1:30(m/m),加酶量7500 U/g、酶解温度55℃、酶解时间3h、pH 7.0时酶解,结果发现,高处理前加木瓜蛋白酶酶解制备的猪骨粉碎率为67.54%,高压处理后加木瓜蛋白酶酶解制备的猪骨粉的粉碎率为72.52%。高压处理后酶解使猪骨的粉碎率提高了6.86%。由此可知,高压处理后酶解有利于提高猪骨粉碎率。
高压处理使骨头软化,骨蛋白变得易于酶解。骨蛋白的酶解导致猪骨的天然结构破坏,出现微小孔洞,这使得猪骨易于被胶体磨粉碎。这可能是高压处理后酶解使猪骨的粉碎率提高的主要原因。
酶解过程受酶解温度、酶解时间、加酶量及pH 影响较大。由于在分析酶解和高压辅助处理次序对猪骨粉碎率影响时,是在固定的酶解条件下进行的。所以,有必要研究最优的酶解工艺,以进一步提高骨粉的粉碎率。
2.2 酶解工艺优化
2.2.1 实验方案
根据文献报道的木瓜蛋白酶酶解猪骨的工艺条件,本研究确酶解温度40.00~70.00℃,酶解时2.00~5.00h,酶解pH4.00~7.00,加酶量5000~12000 U/g为猪骨酶解参数的取值范围。由此获得的响应面实验方案见表2。根据设定的实验方案获得的实验结果见表3。
表2 响应面实验方案及实验结果
组号 | 温度(TEM)/℃ | 时间(TIM)/h | pH | 加酶量(EN)/(U/g) | Y1 |
1 | -1 | -1 | -1 | 1 | 68.47 |
2 | 1 | -1 | -1 | 1 | 71.10 |
3 | -1 | 1 | -1 | -1 | 60.32 |
4 | 1 | 1 | -1 | -1 | 75.56 |
5 | -1 | -1 | 1 | -1 | 63.94 |
6 | 1 | -1 | 1 | -1 | 71.76 |
7 | -1 | 1 | 1 | 1 | 69.69 |
8 | 1 | 1 | 1 | 1 | 73.40 |
9 | -1.68179 | 0 | 0 | 0 | 53.51 |
10 | 1.68179 | 0 | 0 | 0 | 72.49 |
11 | 0 | -1.68179 | 0 | 0 | 74.61 |
12 | 0 | 1.68179 | 0 | 0 | 76.35 |
13 | 0 | 0 | -1.68179 | 0 | 74.50 |
14 | 0 | 0 | 1.68179 | 0 | 77.52 |
15 | 0 | 0 | 0 | -1.68179 | 68.20 |
16 | 0 | 0 | 0 | 1.68179 | 76.65 |
17 | 0 | 0 | 0 | 0 | 75.39 |
18 | 0 | 0 | 0 | 0 | 72.61 |
19 | 0 | 0 | 0 | 0 | 73.50 |
20 | 0 | 0 | 0 | 0 | 72.65 |
21 | 0 | 0 | 0 | 0 | 75.15 |
注:表中TEM 代表酶解温度,℃;TIM 代表酶解时间,h;pH 代表酶解液pH;EN 代表加酶量,U/g;Y1 猪骨的粉碎率。
2.2.2 拟合分析
对表2 中的实验结果进行拟合分析,所得拟合结果的显著性分析见表3。表3中各因素的P值显示,酶解温度(P=0.000207<0.05)和加酶量(P=0.028381<0.05)对猪骨粉碎率的影响显著; 酶解时间( P=0.575944>0.05)和pH(P=0.344393>0.05)对猪骨的粉碎率无显著影响。根据各因素的P值大小可知,各因素对猪骨粉碎率的影响强弱依次为酶解温度>加酶量>pH>酶解时间。
表3中主模型的P=0.003787<0.05显示,建立的模型具有显著性,结合失拟项P=0.075957>0.05、R2=0.96.23说明,所得模型能较好的反映粉碎率与酶解温度、酶解时间、pH及加酶量之间的关系。
表3 各因素及主模型的显著性分析
分类 | 自由度 | 均方差 | F值 | P值 |
TEM | 1 | 275.3345 | 63.57866 | 0.000207 |
TEM | 1 | 1.513798 | 0.349558 | 0.575944 |
pH | 1 | 4.560191 | 1.053013 | 0.344393 |
EN | 1 | 35.70133 | 8.243946 | 0.028381 |
TEM×TEM | 1 | 262.4548 | 60.60455 | 0.000237 |
TEM×TEM | 1 | 9.03125 | 2.085444 | 0.198824 |
TEM×pH | 1 | 5.02445 | 1.160217 | 0.322811 |
TEM×EN | 1 | 34.9448 | 8.069252 | 0.029542 |
TIM×TIM | 1 | 0.73379 | 0.169442 | 0.694908 |
TIM×pH | 1 | 4.210364 | 0.972233 | 0.362201 |
TIM×EN | 1 | 0.764595 | 0.176556 | 0.688982 |
pH×pH | 1 | 2.499539 | 0.577179 | 0.4762 |
pH×EN | 1 | 0.009953 | 0.002298 | 0.963319 |
EN×EN | 1 | 11.01455 | 2.543415 | 0.161866 |
主模型 | 14 | 47.40037 | 10.94542 | 0.003787 |
一次项 | 4 | 82.64388 | 19.08365 | 0.001463 |
二次项 | 4 | 69.76106 | 16.10882 | 0.002315 |
交互项 | 6 | 8.997569 | 2.077667 | 0.197574 |
误差 | 6 | 4.330612 | ||
失拟项 | 2 | 9.411237 | 5.256793 | 0.075957 |
R2 | 0.96.23 |
注:表中TEM 代表酶解温度,℃;TIM 代表酶解时间,h;pH 代表酶解液pH;EN 代表加酶量,U/g
Y1=-219.573+7.328689×TEM+1.289928×TIM+6.115669×pH+0.011851×EN-0.05267×TEM2+0.136131×TEM×TIM-0.099826×TEM×pH-0.000113×TEM×EN+0.289425×TIM2-1.447454×TIM×pH-0.000264×TIM×EN+0.516316×pH2-0.00003×pH×EN-1.982E-7×EN2(1)
注:式中TEM代表酶解温度,℃;TIM代表酶解时间,h;pH代表酶解液pH;EN代表加酶量,U/g;Y1猪骨的粉碎率。
2.2.3 拟合模型验证
为了进一步确定所得模型的可靠性,对酶解工艺进行随机重复试验,所得实际粉碎率(Y1)及根据模型计算的粉碎率(Y2)见表4。表4 中相对误差结果显示,模型的预测结果与实测结果的相对误差均小于5%。由此可见,建立的数学模型很好的反映了酶解温度、酶解时间、加酶量及pH与猪骨粉碎率之间的相互关系。因此,所得模型(1)可用于酶解工艺的优化。
2.2.4 酶解工艺优化
根据式(1)对木瓜蛋白酶酶解高压处理后猪骨的工艺进行优化,得到酶解温度55℃,酶解时间2.01h,酶解pH7.00,加酶量10363 U/g 时,猪骨的粉碎率最高。在该工艺条件下,可以使猪骨的粉碎率达到82.0%。
表4 拟合模型在预测过400 目分样筛骨粉百分率的有效性验证
组号 | 温度/℃ | 时间/h | pH | 加酶量/(U/g) | Y1 /% | Y2/% | 相对误差/% |
1 | 50 | 2 | 4.5 | 7000 | 65.98 | 64.08 | -2.88075 |
2 | 55 | 3 | 6 | 8000 | 74.47 | 74.03 | -0.59594 |
3 | 60 | 3.5 | 6.44 | 10000 | 77.07 | 76.50 | -0.73691 |
4 | 55 | 5 | 7 | 8500 | 75.05 | 74.90 | -0.20553 |
5 | 55 | 3.5 | 5.5 | 8500 | 74.74 | 73.97 | -1.03425 |
注:表中Y1 为过400目分样筛骨粉百分率的真实值;Y2为过400目分样筛骨粉百分率的预测值。
酶解温度、酶解时间、pH及加酶量对猪骨粉碎率的影响也可以通过响应面图看出(图1)。图1显示,猪骨的粉碎率(Y1)随酶解温度(TEM)的变化最明显,其次为加酶量(EN);猪骨的粉碎率(Y1)与酶解时间(TIM)和pH 的变化较酶解温度和加酶量弱。这与酶解温度、酶解时间、pH及加酶量对猪骨粉碎率影响显著性分析结果一致。
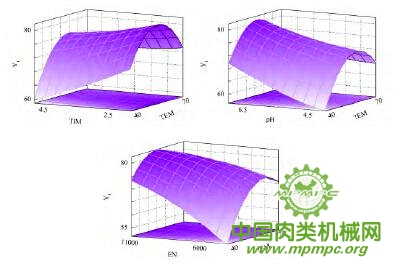
图1 酶解最优工艺的响应面
注:图中TEM代表酶解温度,℃;TIM 代表酶解时间,h;pH 代表酶解液pH;EN 代表加酶量,U/g;Y1 猪骨的粉碎率。
2.3 骨粉中钙、磷含量比较
为了分析高压和酶解辅助处理对猪骨中钙、磷含量的影响,对新鲜猪骨及制备的猪骨粉中钙、磷含量分别测定,得出新鲜猪骨的钙含量为14.00%,高压、酶解处理后制备的骨粉的钙含量为13.60%,辅助处理对猪骨中钙含量的损失率为2.86%。新鲜猪骨含磷量7.35%,高压、酶解处理后制备的骨粉含磷量为7.10%,辅助处理对猪骨中损失率为3.40%。
比较新鲜猪骨和辅助处理后骨粉中钙和磷的比值,分别为1.90 和1.91,钙磷比约等于2。由钙和磷的损失率分别为2.86%和3.40%,并结合钙、磷比约等于2的结果可知,高压、酶解辅助制备超微骨粉辅助处理能较好地保留新鲜骨粉的钙磷含量。
3 结论
高压处理猪骨后酶解较高压处理前酶解所得骨粉的粉碎率高。对高压处理后酶解工艺采用响应面法优化,得出酶解温度为55℃,酶解时间为2.01h,酶解pH7.00,加酶量为10363 U/g 时所得猪骨的粉碎率最高为82.0%,比未优化前提高了9.45%。对粉碎前后猪骨中的钙磷含量分析,得出高压和酶解辅助粉碎对猪骨中的钙磷含量损失较小。因此,高压和酶解辅助处理,可有效提高猪骨的粉碎率。